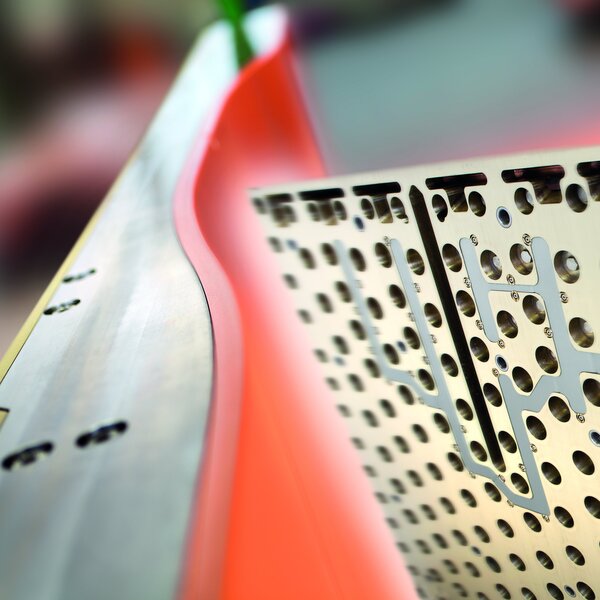
Known worldwide for outstanding Quality
As the market leader for complex, customer-specific casting moulds, cunova is the preferred supplier of leading companies involved in the melting and casting of ferrous and non-ferrous metals. Aided by integrated optical measurement technology and sensors, the copper and copper alloy casting moulds boost product quality and make the casting process even more productive.

Casting
For casting machines, we manufacture a comprehensive, customised range of casting moulds/moulds made from various copper alloys with coatings that are suitable for the high mechanical and thermal loads.
cunova optimises the geometry and cooling of existing casting moulds to improve the product quality and service life of moulds.
Overview casting
We customise mould plates for horizontal and vertical continuous casting systems to suit the requirements of the respective system - both in terms of design and coating.
For thin-slab casting systems with funnel-shaped mould plates, we have developed the AFM (Advanced Funnel Mould) mould, which reliably dissipates heat even at high casting speeds. The innovative surface-cooling design provides particularly homogeneous temperature distribution.
Furthermore, the ATSM (Advanced Thin Slab Mould) mould plates offer improved ease of maintenance.
For continuous casting of billets, we manufacture the entire range of mould tubes for the geometries and dimensions commonly used today - from small rectangular to large-format round cross-sections. In addition, we develop mould tubes with optimised conicities and special internal geometries, such as the WAVE® or the textured mould.
Our ABBM (Advanced Beam Blank Mould) mould plates for casting blooms - for example for double-T beams and rails - optimise the quality of the cast sections: Cooling water flows through the gap between the copper plate and the steel support structure, producing very homogeneous temperature distribution.
cunova casting wheels are used worldwide to produce aluminium and copper wire. As they are constantly coming into contact with molten metal, they are subject to high alternating thermal and mechanical loads. Our high-end copper materials such as CuAg, ELBRODUR® G or ELBRODUR® GF can withstand this extreme stress and prolong the service life of the casting wheel.
In thin-strip casting of non-ferrous metals, the casting sleeves of the two counter-rotating rolls are subjected to high alternating thermal and mechanical loads. The high thermal conductivity and superior mechanical properties of our copper materials prevent cracking and ensure a long service life.
In twin-belt casting, the dam blocks are subjected to extreme stresses as the belt opens and closes during each cycle. Our OSNISIL® G alloy is not only extremely strong but also highly resistant to the extreme thermal shocks to which the dam blocks are subjected.
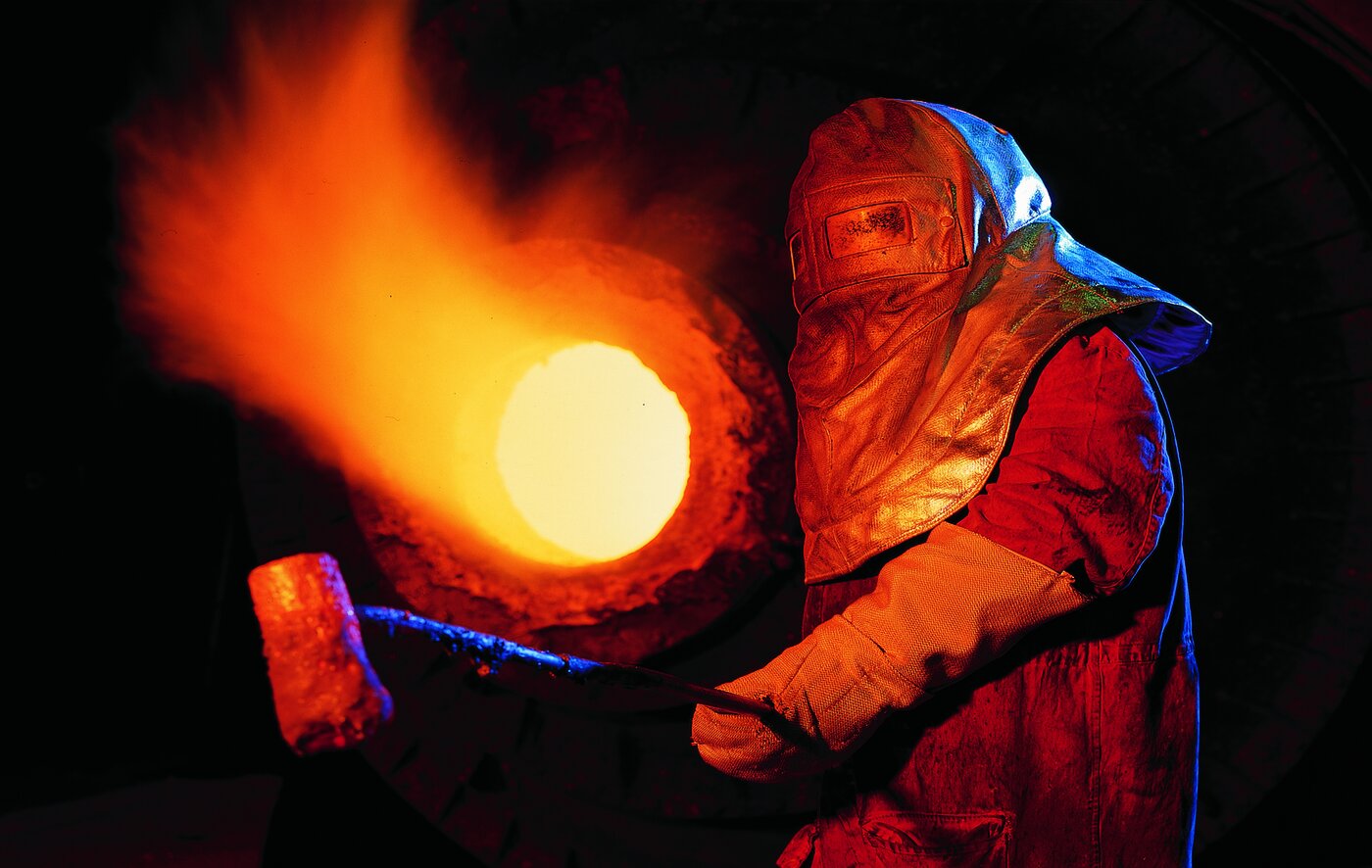
Melting
Copper plays a key role in the melting of metals: It dissipates heat quickly and can withstand thermal stress.
Our unique combination of expertise, long experience, production know-how and service for the use of copper in metal production and processing makes us a highly skilled partner when it comes to all aspects of melting.
Melting Overview
In modern blast furnaces for pig iron production, our copper staves are a tried and tested method for efficient cooling. We pioneered their development and hold the basic patent.
The profiled copper staves equipped with deep-drilled cooling channels ensure the controlled evacuation of process heat. In combination with high-strength ceramic materials, they offer maximum temperature resistance, media resistance and abrasion resistance.
For the remelting of special alloys and titanium in electric arc or vacuum arc furnaces, we produce seamless forged crucibles from copper. They have superior mechanical strength, deliver excellent dimensional stability and have a long service life.
Our finned tubes in oxygen-free copper cool the furnace walls when remelting metals in electric arc furnaces. The tubes are highly efficient at dissipating heat, have a long service life and are easy to install.

Engineering & Service
Each mould must be individually adapted to the casting conditions, taking account of the alloy, cross-section, casting speed and so on. That is why we offer extensive support in mould design and optimisation.
Whether it's higher casting speeds, different dimensions or improving product quality, We offer comprehensive engineering and consultancy services for all aspects of moulds and, if required, we can also undertake detail engineering based on the design plans of the equipment manufacturer.
Our maintenance and repair service for mould plates and tubes includes everything from professional reworking and repair and possible re-coating, right up to full reconditioning of the entire mould. We offer these services to our customers through our worldwide network of service centres.